What is Porosity in Welding: Ideal Practices for Avoiding Permeable Welds
Porosity in Welding: Identifying Common Issues and Implementing Finest Practices for Avoidance
Porosity in welding is a pervasive problem that usually goes unnoticed till it triggers considerable issues with the integrity of welds. This usual problem can compromise the stamina and durability of welded frameworks, posturing security risks and causing pricey rework. By understanding the root triggers of porosity and implementing efficient prevention techniques, welders can substantially enhance the top quality and reliability of their welds. In this conversation, we will discover the vital factors adding to porosity development, analyze its harmful results on weld efficiency, and discuss the very best methods that can be embraced to reduce porosity occurrence in welding processes.
Typical Reasons For Porosity
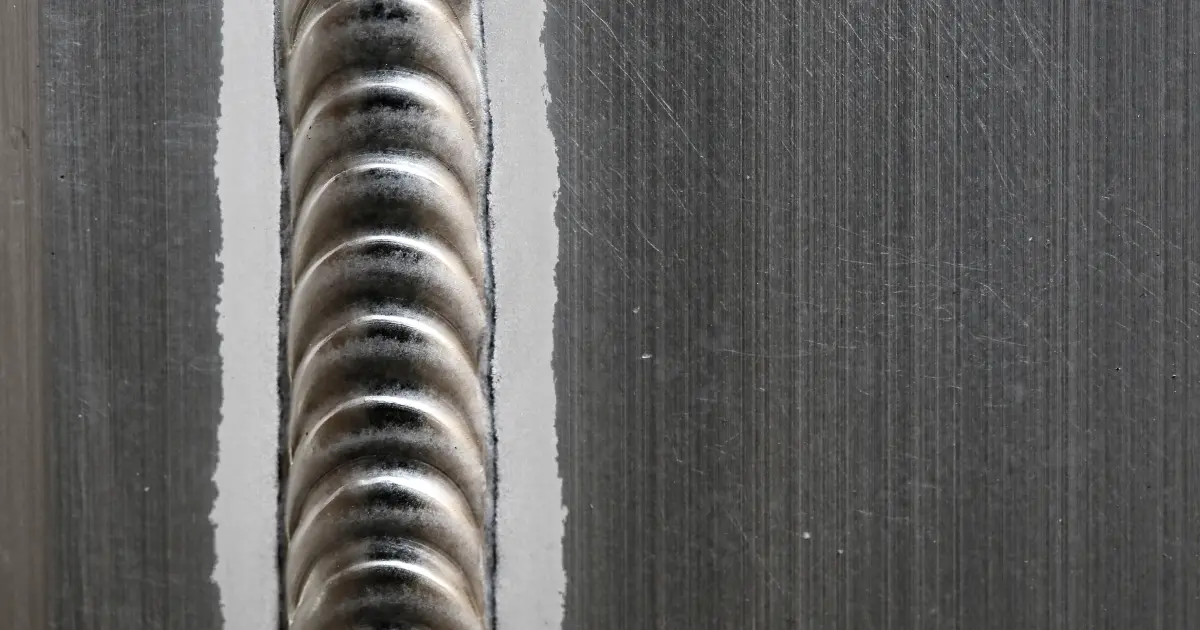
Another constant culprit behind porosity is the presence of contaminants externally of the base metal, such as oil, oil, or corrosion. When these pollutants are not effectively gotten rid of before welding, they can vaporize and become trapped in the weld, causing defects. Moreover, utilizing unclean or damp filler products can present impurities right into the weld, adding to porosity concerns. To reduce these typical reasons of porosity, complete cleansing of base metals, proper shielding gas selection, and adherence to ideal welding parameters are essential practices in achieving premium, porosity-free welds.
Impact of Porosity on Weld High Quality

The presence of porosity in welding can dramatically endanger the architectural honesty and mechanical residential or commercial properties of welded joints. Porosity develops gaps within the weld metal, weakening its total stamina and load-bearing capacity. These spaces function as stress and anxiety focus factors, making the weld much more prone to splitting and failing under applied loads. In addition, porosity can reduce the weld's resistance to corrosion and other environmental factors, even more reducing its durability and performance.
Among the primary consequences of porosity is a decrease in the weld's ductility and durability. Welds with high porosity degrees have a tendency to exhibit reduced influence strength and minimized capability to flaw plastically before fracturing. This can be especially worrying in applications where the welded components are subjected to dynamic or cyclic loading problems. Additionally, porosity can impede the weld's capability to efficiently transmit pressures, bring about early weld failing and possible security hazards in crucial structures.
Best Practices for Porosity Avoidance
To boost the architectural stability and quality of welded joints, what certain procedures can be executed to lessen the incident of porosity throughout the welding procedure? Utilizing the appropriate welding method for the particular product being bonded, such as changing the welding angle and weapon placement, can better protect against porosity. Routine examination of welds and instant removal of any kind of concerns determined during the welding procedure are vital techniques to prevent porosity and create high-quality welds.
Importance of Proper Welding Strategies
Carrying out appropriate welding methods is critical in making sure the structural stability and quality of bonded joints, building on the structure of efficient porosity prevention measures. Welding strategies directly affect the overall stamina and sturdiness of the bonded framework. One key element of proper welding methods is maintaining the correct warmth input. Excessive warmth click now can cause boosted porosity due to the entrapment of gases in the weld pool. On the other hand, inadequate warmth might result in insufficient fusion, creating possible powerlessness in the joint. Furthermore, making use of the appropriate welding specifications, such as voltage, present, and take a trip speed, is critical for attaining audio welds with marginal porosity.
Furthermore, the option of welding procedure, whether it helpful resources be MIG, TIG, or stick welding, ought to line up with the specific needs of the job to make sure ideal outcomes. Appropriate cleansing and preparation of the base metal, as well as selecting the right filler material, are additionally necessary parts of efficient welding methods. By adhering to these finest methods, welders can decrease the danger of porosity formation and create top notch, structurally audio welds.
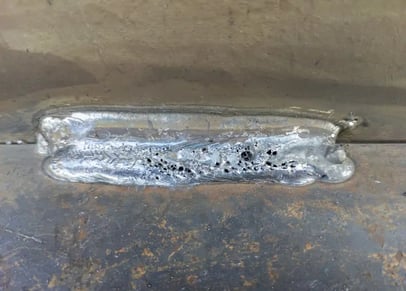
Evaluating and High Quality Control Measures
Quality assurance steps play an important function in validating the stability and reliability of bonded joints. Testing procedures are necessary to check my source detect and prevent porosity in welding, making sure the stamina and sturdiness of the end product. Non-destructive screening approaches such as ultrasonic testing, radiographic screening, and visual inspection are commonly utilized to recognize possible defects like porosity. These methods permit for the assessment of weld high quality without jeopardizing the honesty of the joint. What is Porosity.
Performing pre-weld and post-weld examinations is additionally crucial in keeping quality control criteria. Pre-weld inspections involve confirming the products, devices setups, and tidiness of the workplace to stop contamination. Post-weld examinations, on the other hand, evaluate the final weld for any kind of problems, consisting of porosity, and confirm that it meets defined standards. Carrying out a thorough quality assurance strategy that consists of thorough screening procedures and examinations is critical to decreasing porosity issues and ensuring the total top quality of bonded joints.
Verdict
In verdict, porosity in welding can be a typical concern that impacts the high quality of welds. By determining the usual reasons of porosity and implementing best methods for prevention, such as appropriate welding strategies and screening measures, welders can make sure high quality and trustworthy welds. It is vital to focus on avoidance methods to decrease the occurrence of porosity and keep the stability of welded structures.